Customer orders
Add new position
If the webshop view option is active, clicking the button opens the item list. Clicking on the shopping basket button displays the item with the quantity 1 as an order item. The quantity may only be entered as an integer value. Individual items can be deleted using the rubbish bin button.
Finally, the entries must be saved using the Add customer order position button.
Without the webshop view, the items are entered individually; the editor corresponds to that for incoming goods lists.
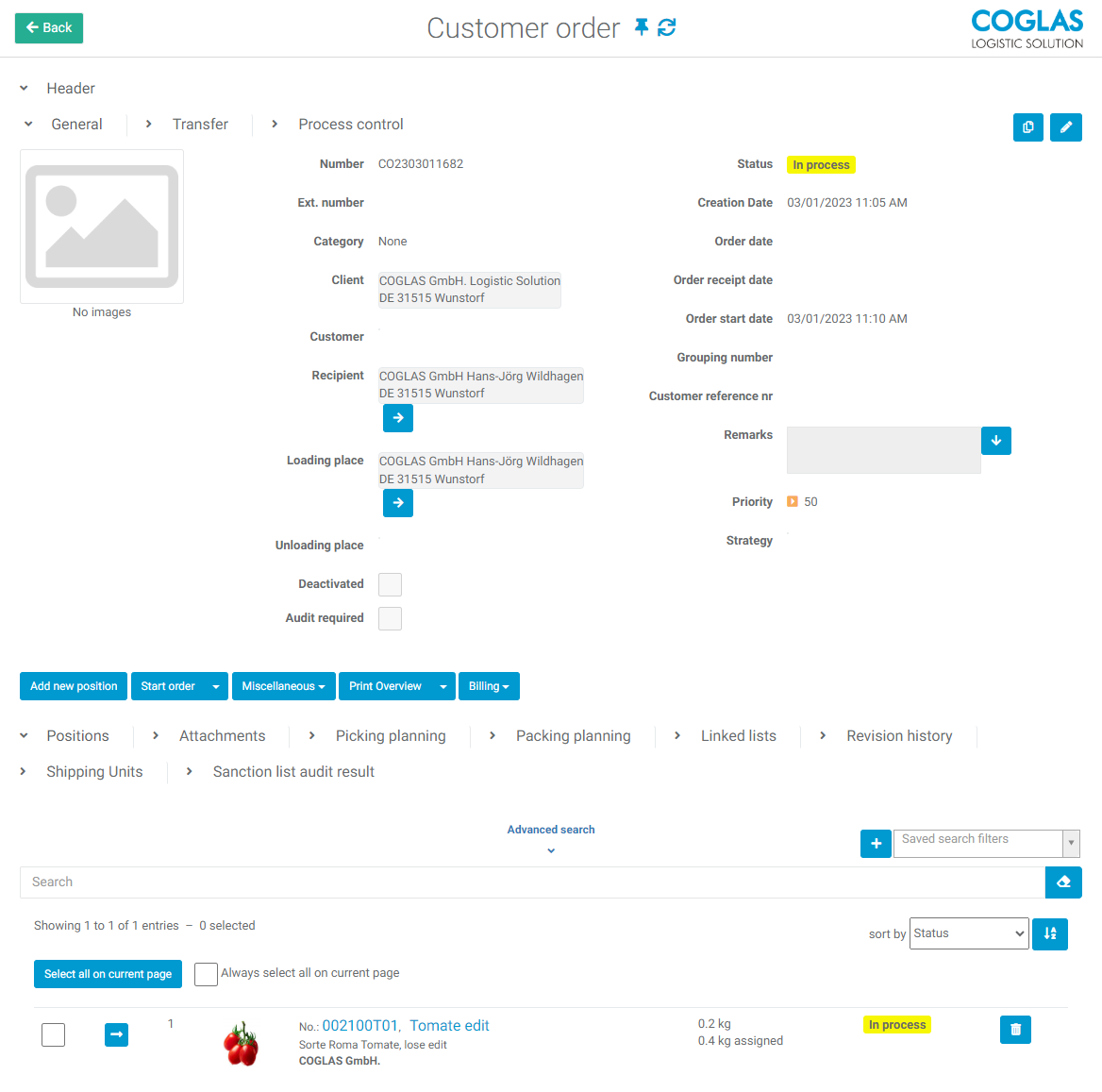
Start order
As soon as a customer order including at least one item has been entered, the ‘Start order’ button can be used to automatically assign stock reservations based on the selected strategy and create corresponding transport & picking orders.
Depending on the configuration, one of the following scenarios is set as the default for the Start order function. Alternatively, the other option can be called up for each order using the small arrow next to the ‘Start order’ button.
Start order for staging:
Both picking orders and transport orders for full pallets are generated, all of which have staging as their destination. The goods can therefore be consolidated from the different storage areas and prepared for dispatch if there is enough free space.
Start order for picking:
Only picking orders are generated. Transport orders for full pallets are only generated when loading starts and point directly from the current storage location of the SU to the goods issue gate or the loading area. This skips the interim storage in the staging area - particularly helpful in the event of capacity bottlenecks in the loading area.
Volume planning
The volume calculation for the requirement of picking and packing storage units is only triggered when the order is started. The aim is always to have as few storage units in total as possible and at the same time to use the most suitable container sizes.
Only load carriers that are labelled ‘Suitable for order picking’ are used for order picking planning. Only the requirements of a customer order that are to be provided via order picking are taken into account. Full pallets are therefore not taken into account!
The calculated unit load requirement is also used as the basis for setting up the pick trolley. Further information on the multi-pick can be found in the chapter Transport → Picking.
Only loading aids that are labelled ‘Suitable for packaging’ are used for packaging planning. All items and quantities of the customer order are taken into account when calculating the total volume.
Methodology of the calculation:
The space requirement of an item is normalised: the largest dimension (length, width or height) is checked against the storage unit.
Items that do not fit into the largest container or whose master data is not complete are collected in a SU of the largest type.
Items with a nesting factor are also taken into account when calculating the volume.
Customer order position
In the detailed view of the item, specifications for stock determination can be made for the respective item. Entered values, e.g. batch, must be congruent between the specification and the desired stock. If there is no stock with the entered batch in the warehouse, the order cannot be started - no suitable goods are available.
Manual stock allocation:
In addition to automatic replenishment, it is also possible to allocate specific stocks to an order on a dedicated basis.
Whole storage unit: A specific, whole container should be reserved for the required item. Processing takes place via transport
Picking: The required item is to be picked from a specific source SU. Processing takes place via picking.
Accept shortages:
In the event of missing parts (not enough stock available) or at manual request, items can be finalised and thus under-delivered. This is possible for the total quantity as well as for partial quantities of the item.
Manually closed positions cannot be reopened once the security enquiry has been confirmed!
Billing
Provided Services
Additional activities can be entered that are to be taken into account in the course of billing. The desired services must first be entered in the billing configuration before they can be used in the customer order. Further information can be found in the chapter Billing → Warehouse services.
Billing
Opens the invoice for the current sales order and displays all relevant items. Further information can be found in the Billing chapter.
→ back to COGLAS processes
→ back to COGLAS menu