Tugger train cockpit
General
The tugger train control system enables the delivery of loading aids / empties to production lines at regular intervals and/or at one-off delivery times.
The stations and products can be created in the setup.
A loading aid, quantity and interval can be defined for the products. For the stations, the product, the next delivery time and the status of the station can then be set to active or inactive.
The cockpit provides a timetable for the train, as well as complete control over the loading and delivery of a station.
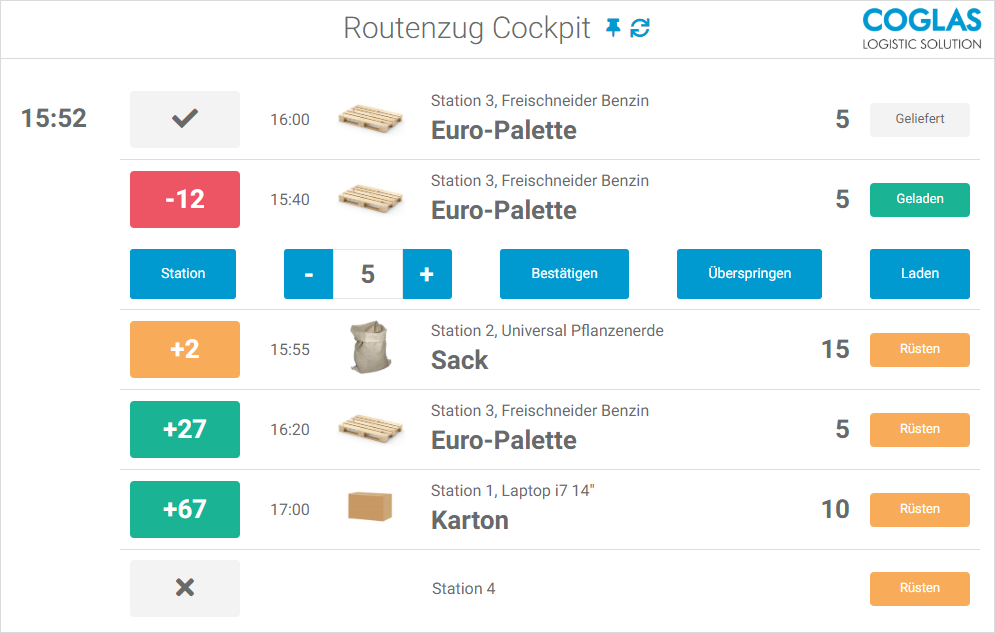
Tugger train product
The tugger train form in the item master data allows you to create a product for the specific item.
A product consists of a loading aid, a quantity and the delivery interval.
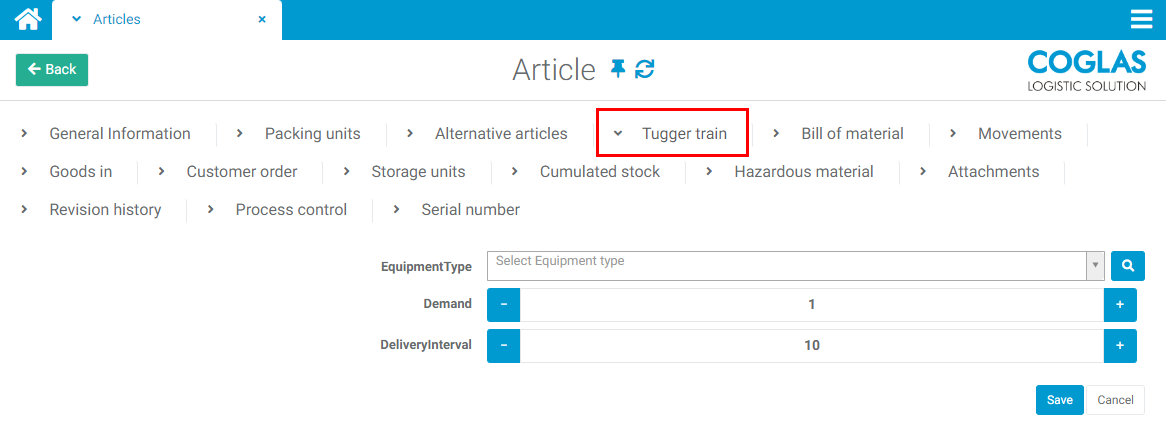
Tugger train stations
The Stations form shows an overview of existing stations and allows you to edit and add stations.
The following parameters must be maintained when creating stations:
Name of the station
Product to be delivered
Selection from the types created in the master data (Master data ‘ Article ’ Route train)
Cumulative demand (optional)
Initial value of the first delivery or corrected demand quantity at any time after activation
Status of the station
active = When this value is set, a schedule entry with the current time plus delivery interval is created as a date in the Planned status.
As soon as a schedule entry changes from the Planned status to the Loaded or Delivered status, the system generates a new entry in the Planned status.
Idle = No new schedule entries are generated when the status changes.
Planned delivery (optional)
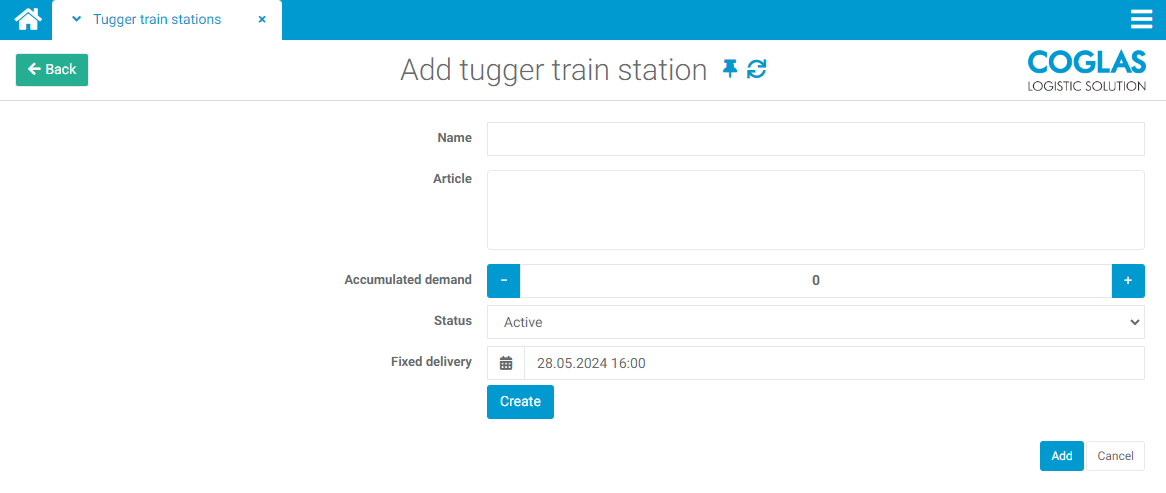
Tugger train cockpit
The cockpit displays the next delivery dates of the tugger train and offers the option of triggering various status messages. For each station, only the next delivery is displayed as long as it is unprocessed, i.e. not prepared, skipped or delivered.
The deliveries configured in the stations are sorted in ascending order from top to bottom in the cockpit's timetable display (next delivery time is displayed at the top).
The delivery times can either be automatically generated deliveries based on the selected time interval or one-off deliveries.
The remaining time until the planned delivery is highlighted in colour. The colour scheme is defined as follows:
Status | Description |
---|---|
![]() | Delivery date scheduled, manually or via interval. |
![]() | The requirement has been received at the point of origin and is on the train (delivery is expected shortly). |
![]() | The delivery has been successfully completed. The item has been completed. |
The following functions are available for the individual delivery entries:
Status | Description |
---|---|
![]() | Delivery date scheduled, manually or via interval. |
![]() | The requirement has been received at the point of origin and is on the train (delivery is expected shortly). |
![]() | The delivery has been successfully completed. The item has been completed. |
![]() | The delivery could not be carried out. The required quantity is still open. |
When loading, the quantity to be loaded is prefilled with the values from the master data, but this can be corrected upwards or downwards.
In the event of an underdelivery, the missing quantity is automatically added to the next outbound delivery.
Edit tugger train station
Click on the Station button to open the menu for the station. In this menu, you can stop and start the stop-off point and create an additional delivery date.
If a station is stopped, you can change the product either by scanning or manually selecting it. This function can also be customised via the user roles.
The barcode used for the scan is the EAN13 barcode from the article master data.
→ back to COGLAS processes
→ back to COGLAS menu